Thermoforming: The Future of Cost-Effective, Scalable Manufacturing
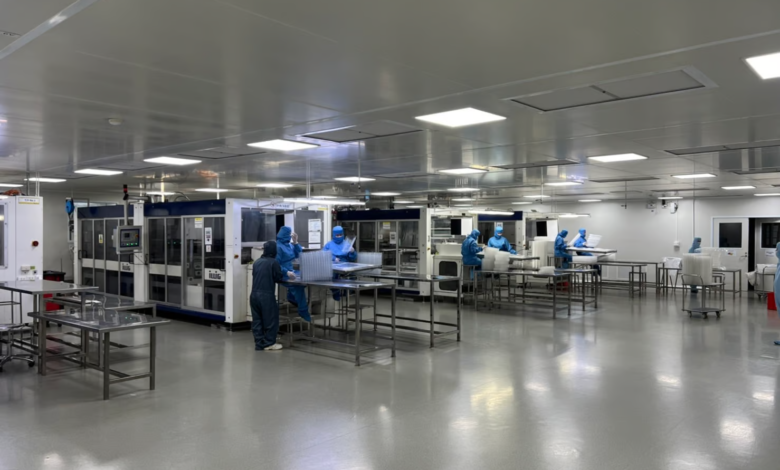
Introduction
Thermoforming has emerged as a go-to manufacturing method for industries requiring high-quality plastic components at an affordable cost. From automotive panels to medical trays and food packaging, thermoforming provides a versatile, scalable, and efficient way to shape plastic materials into durable products.
But what makes thermoforming so effective compared to traditional manufacturing techniques like injection molding, machining, or 3D printing? And how can companies optimize the process to enhance quality, reduce costs, and maximize efficiency?
This article explores the fundamentals of thermoforming, compares it to other manufacturing methods, and examines key design principles that ensure superior product performance and cost savings.
1. What Is Thermoforming? A Manufacturing Revolution
Thermoforming is a plastic molding process that involves heating a thermoplastic sheet until it becomes pliable and then shaping it over a mold. Once the sheet cools and solidifies, excess material is trimmed away, leaving behind a functional, lightweight, and durable part.
Why Choose Thermoforming?
Thermoforming is particularly valuable for medium- to high-volume production runs, offering significant advantages over other plastic manufacturing methods:
- Lower Tooling Costs – Thermoforming molds are significantly less expensive than injection molding dies, making it ideal for smaller production runs and rapid design changes.
- Faster Production Cycles – Compared to machining, thermoforming can produce parts more quickly and with less material waste.
- Scalability – Unlike 3D printing, which is better suited for prototyping, thermoforming is highly scalable, making it a cost-effective option for mass production.
- Material Versatility – Thermoforming supports a wide range of thermoplastics, from high-impact polystyrene (HIPS) to polycarbonate (PC) and polyethylene terephthalate glycol (PETG).
How Does Thermoforming Compare to Other Methods?
Manufacturing Method | Advantages | Limitations |
Thermoforming | Low tooling costs, fast production, material flexibility | Less detail than injection molding, trimming required |
Injection Molding | High precision, repeatability, no trimming required | Expensive tooling, high initial setup costs |
Machining (CNC, Milling) | Extreme accuracy, excellent for high-strength parts | Slow, high material waste, expensive |
3D Printing | Rapid prototyping, complex geometries, minimal setup cost | Slow, not ideal for mass production, expensive for large parts |
While injection molding excels at producing high-detail components in large volumes, its tooling costs can be prohibitive. Thermoforming bridges the gap, offering a balance of affordability, speed, and durability.
2. The Thermoforming Process: Step-by-Step Breakdown
The thermoforming process involves three key steps:
1️⃣ Heating – A thermoplastic sheet is heated until it reaches a pliable state, allowing it to be shaped.
2️⃣ Forming – The heated sheet is then pressed over or into a mold, shaping it into the desired form.
3️⃣ Trimming & Finishing – Excess material is removed, and edges are refined for a smooth, finished part.
Types of Thermoforming: Which One Is Right for You?
There are several variations of the thermoforming process, each suited for different applications:
- Vacuum Forming – Uses a vacuum to suction the plastic sheet against the mold, ensuring high detail. Ideal for packaging, panels, and enclosures.
- Pressure Forming – Adds compressed air to push the sheet onto the mold, creating sharper details and crisper textures—great for consumer electronics and automotive interiors.
- Drape Forming – The plastic is laid over a mold and shaped using gravity and slight pressure, making it ideal for large, simple curves in aerospace and industrial applications.
Trimming & Finishing: The Key to High-Quality Parts
Once the plastic has been formed, excess material needs to be removed and refined. Three primary trimming methods ensure a precise, professional finish:
- CNC Trimming – Automated and highly accurate, best for high-precision parts.
- Die Cutting – A fast and cost-effective method for high-volume, thin-gauge plastic production.
- Hand Trimming – Ideal for prototyping and small runs, though less precise.
By choosing the right forming and trimming method, manufacturers can create cost-effective, functional, and aesthetically appealing thermoformed parts.
3. Key Design Principles for Thermoforming: Maximizing Quality and Cost Efficiency
Thermoforming imposes unique design constraints that differ from injection molding or machining. Because parts are shaped from a single sheet, manufacturers must consider thickness distribution, mold design, and part removal to ensure optimal manufacturability.
3.1 Draft Angles: Preventing Sticking & Mold Damage
One of the most crucial design elements in thermoforming is draft angle selection, which ensures parts can be easily removed from the mold without sticking, warping, or tearing.
- Male Molds (Positive Molds) → Require 3–5° of draft to accommodate shrinkage.
- Female Molds (Negative Molds) → Require only 1–2° of draft, since plastic shrinks away from the mold.
Without sufficient draft, parts can become trapped, leading to defects, production delays, and increased costs.
3.2 Male vs. Female Molds: Controlling Material Thinning
Choosing male or female molds affects surface accuracy, material thickness, and tooling costs.
Mold Type | Pros | Cons |
Male (Positive) Molds | Better thickness control, cost-effective | Surface texture is determined by the plastic sheet, not the mold |
Female (Negative) Molds | More precise external detail, high aesthetic accuracy | More material thinning, higher mold costs |
For structural components, male molds are preferred for better thickness control. If surface detail is the priority, female molds are the best option.
3.3 Multi-Up Tooling: Improving Cost Efficiency
By forming multiple parts per sheet, manufacturers can reduce cycle times, labor, and material waste.
Tooling Type | Parts per Cycle | Efficiency Gain |
1-up Tooling | 1 | Ideal for low-volume production |
2-up, 4-up Tooling | 2–4 | Cuts labor costs by 50–75% |
8-up, 16-up Tooling | 8+ | Maximizes material yield for high-volume runs |
For example, if a machine produces 5 sheets per hour, a 1-up tool yields 5 parts/hour, while a 4-up tool yields 20 parts/hour—a fourfold increase in efficiency!
Thermoforming the Future: How to Get Started
Thermoforming continues to evolve, with advancements in automation, materials, and sustainability shaping the industry. As manufacturers seek cost-effective, high-volume solutions, thermoforming stands out as a proven, scalable method that balances quality and affordability.
Start Your Thermoforming Project with RapidMade
At RapidMade, we specialize in precision thermoforming solutions, helping manufacturers optimize designs, reduce costs, and improve efficiency. Whether you need low-volume prototyping or full-scale production, our team of experts delivers custom solutions tailored to your needs.
📞 Contact us today to explore how thermoforming can benefit your business!
📩 Email: info@rapidmade.com
🌐 Website: rapidmade.com
By partnering with RapidMade, you can take advantage of advanced thermoforming technology, expert design support, and efficient production methods—ensuring superior results at the best cost.