Mastering Industrial Cooling Tower Maintenance: A Proven Guide to Efficiency and Safety
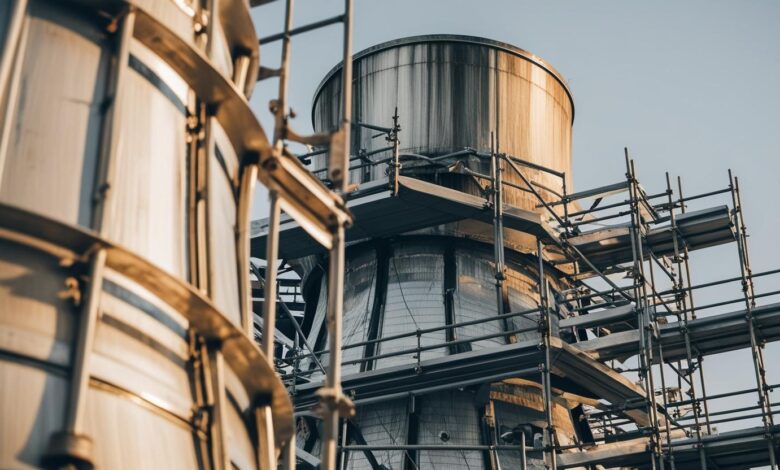
Introduction: My Journey in Industrial Cooling Systems
Over the past 15 years, I’ve worked closely with industrial facilities—manufacturing plants, power stations, and data centers—where cooling towers are the backbone of operational continuity. One memorable client, a steel mill in Ohio, faced a $50,000 shutdown because their cooling tower’s fill material was eroded, causing a 30% drop in heat dissipation. This isn’t an isolated incident. The U.S. Department of Energy (DOE) estimates that improper maintenance costs industrial facilities up to $2 billion annually in lost productivity and energy waste.
Industrial cooling towers operate under extreme conditions: high temperatures, corrosive water, and constant wear. Yet, with the right maintenance strategy, you can avoid these costly pitfalls. This guide blends my on-the-ground experience with data-driven insights to help you optimize your system.
Why Industrial Cooling Towers Need Specialized Maintenance
Industrial cooling towers are mission-critical, often handling 100+ tons of heat daily. Their failure can halt production lines, damage machinery, and even endanger worker safety.
Key Industrial-Specific Challenges:
- Scale Buildup: Minerals in hard water form scale at 3–5 times faster rates in high-heat environments.
- Corrosion: Aggressive chemicals and abrasive particles accelerate metal degradation.
- Microbial Growth: Legionella bacteria thrive in warm, stagnant water—industrial towers provide ideal conditions.
The CDC warns that improper maintenance increases Legionella risk, which caused 5,000+ hospitalizations annually in the U.S. alone. Meanwhile, the EPA mandates strict water quality standards to prevent environmental contamination.
Critical Components for Industrial Towers
Industrial systems demand rigorous attention to these key areas:
1. Water Quality Management
Industrial water often contains contaminants like silica, chloride, and suspended solids. Poor water treatment can lead to:
- Scale Formation: Reduces heat transfer efficiency by up to 20% (DOE).
- Corrosion: Pitting in pipes costs facilities $12 billion yearly in repairs (NACE International).
My Solution:
- Install a continuous water treatment system with chemical feeders and pH sensors.
- Follow the EPA’s guidelines for industrial water quality (linked below).
- Use biocides and dispersants to combat microbial growth.
2. Fill and Distribution System
The fill (heat exchange media) is where 70% of heat dissipation occurs. In industrial towers, this component faces constant erosion from water flow and debris.
- Insight: I’ve seen towers regain 15% efficiency after replacing PVC fill with more durable HDPE material.
- Action: Inspect fills monthly for erosion or blockages. Clean nozzles weekly to ensure even water distribution.
3. Mechanical Components
Fans, motors, and drives endure relentless use. Misalignment or wear can cause:
- Energy Waste: A 10% drop in fan efficiency increases energy use by 20% (DOE).
- Premature Failure: Bearings and belts require monthly lubrication and tension checks.
4. Drift and Basin Maintenance
Drift eliminators reduce water loss, while basins collect recirculated water. Industrial towers lose 0.1–0.5% of water daily via drift, costing thousands in water waste.
- Tip: Clean drift eliminators biweekly and skim basins daily to prevent algae buildup.
My Step-By-Step Industrial Maintenance Plan

Here’s how I ensure industrial towers run smoothly:
Daily Checks
- Monitor water levels, pH, and flow rates.
- Inspect for unusual vibrations or leaks.
Weekly Tasks
- Test water for conductivity, chlorine, and total dissolved solids (TDS).
- Clean strainers and spray nozzles.
Monthly Deep Cleaning
- Pressure-wash fill materials and basins.
- Audit chemical feed systems.
Quarterly Mechanical Inspection
- Check fan alignment, belt tension, and bearing lubrication.
- Replace worn gaskets or seals.
Annual Overhaul
- Conduct a full system pressure test.
- Replace aged components (e.g., nozzles, drift eliminators).
For a detailed, photo-rich guide that walks you through these steps, click here . This checklist has saved my industrial clients $100,000+ annually in energy and repair costs.
Common Industrial Issues & Fixes
1. Scale Accumulation
- Cause: High mineral content in feedwater.
- Fix: Use a water softener and phosphate-based inhibitors.
2. Legionella Outbreaks
- Cause: Stagnant water or inadequate biocide use.
- Fix: Follow the CDC’s Legionella control guidelines here .
3. Air Imbalance
- Cause: Clogged louvers or misaligned fans.
- Fix: Clean louvers and recalibrate fan angles quarterly.
4. Severe Corrosion
- Cause: Acidic water or inadequate inhibitors.
- Fix: Add corrosion inhibitors like zinc or molybdate.
The ROI of Industrial Cooling Tower Maintenance
Investing in maintenance isn’t just about avoiding breakdowns—it’s about long-term savings:
- Energy Savings: A well-maintained tower uses 15–25% less energy (DOE).
- Equipment Lifespan: Regular care can double tower lifespan (from 10 to 20+ years).
- Compliance: Avoid EPA fines by meeting water discharge standards.
Final Thoughts: Protect Your Industrial Operations
Industrial cooling towers are the unsung heroes of heavy manufacturing and energy production. Neglecting their care is a gamble with your bottom line and safety. By following this plan, referencing resources like the EPA’s industrial water management guide , and leveraging tools like my maintenance checklist, you’ll ensure reliability and compliance.
Tom Pence is a Cooling Tower specialist with 15+ years in industrial cooling systems. His clients include Fortune 500 companies and utilities, where he’s slashed energy costs by 30% through preventive maintenance.