Understanding Physical Vapor Deposition: A Friendly Guide to PVD vs. CVD
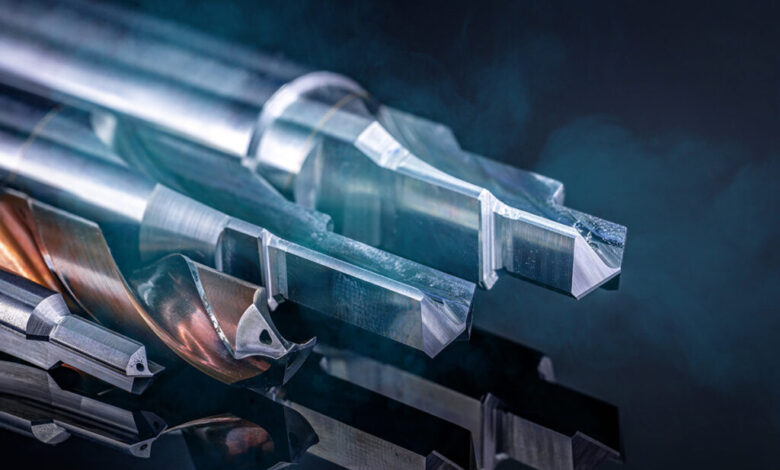
Let’s Talk About Physical Vapor Deposition
Okay, let’s start with a fun fact: many of the shiny, strong, and long-lasting things you use every day might be thanks to a cool process called physical vapor deposition, or PVD for short. Sounds technical? Don’t worry — we’ll walk through it together in a super simple, easy-to-understand way.
So, what is physical vapor deposition, really?
Think of it like this: Imagine you want to cover something with a really thin, strong, and smooth layer — kind of like wrapping a gift, but on a microscopic level. With PVD, we take a solid material (usually metal), turn it into vapor, and then let it settle onto another surface to form a super thin coating.
This process happens in a vacuum (that means no air inside the machine), which keeps everything clean and controlled. That’s what makes PVD coating so precise and effective. And get this — the coatings are often only a few atoms thick! Crazy, right?
But even though it’s so thin, the result is tough, durable, and looks amazing. That’s why PVD is used in so many industries like electronics, medical tools, watches, aerospace, and even cars.
Why Is PVD So Popular These Days?
One big reason is that physical vapor deposition is eco-friendly. Unlike some older coating methods that use harmful chemicals or create toxic waste, PVD keeps it clean and green.
It also works at lower temperatures, which is a big win. That means it can be used on delicate materials like plastic, glass, and even certain types of rubber without damaging them.
Other benefits include:
- Super high precision
- Consistent, even coating
- Great for wear resistance
- Long-lasting results
- Visually stunning finishes (like gold, black, or rainbow effects)
- No harmful byproducts
All that, and it helps manufacturers save time, reduce waste, and create better-performing products. What’s not to love?
How Does Physical Vapor Deposition Actually Work?
Here’s a simple step-by-step to explain how the physical vapor deposition process works:
- The object to be coated (called the substrate) is cleaned and placed inside a vacuum chamber.
- A solid coating material (like titanium, chromium, or gold) is also placed inside.
- The chamber is sealed and air is removed to create a vacuum.
- The coating material is heated using techniques like sputtering or evaporation.
- It turns into vapor and travels across the vacuum to the surface of the object.
- The vapor then condenses — or turns back into solid — on the surface, forming a thin film.
That’s it! No extra steps, no messy chemicals. Just a clean, smooth, and super effective process. It’s kind of like magic — but with science.
Let’s Talk About Chemical Vapor Deposition
Now that we’ve got a solid understanding of PVD, let’s meet its cousin — chemical vapor deposition, or CVD.
CVD is also a way to coat materials with a thin film, but instead of using just heat and vapor like PVD, it involves chemical reactions. It uses gases that react with the surface of the item being coated.
Here’s how it works:
- The object is placed in a hot chamber.
- A gas mixture is introduced, and it reacts with the surface or with itself.
- This reaction forms a solid coating right on the object’s surface.
- The byproducts (extra gas, waste, etc.) are removed from the chamber.
CVD is great for making ceramic coatings, semiconductors, and solar panels. But it does have a few drawbacks. It usually requires higher temperatures — sometimes over 1000°C — and often produces chemical waste that needs proper disposal.
What’s the Real Difference Between PVD and CVD?
Let’s break it down in a friendly way. While physical vapor deposition and chemical vapor deposition both aim to do the same thing — coat surfaces — they go about it in totally different ways.
Here’s an easy comparison chart:
Feature | Physical Vapor Deposition (PVD) | Chemical Vapor Deposition (CVD) |
Type of Process | Physical (no chemical reaction) | Chemical (uses reactive gases) |
Temperature | Lower (good for delicate materials) | Higher (often 800-1200°C) |
Materials Used | Metals, alloys | Ceramics, silicon, carbon |
Waste & Emissions | Minimal, eco-friendly | More waste, chemical byproducts |
Surface Finish | Very precise, smooth | Slightly less controlled |
Typical Uses | Watches, tools, electronics | Semiconductors, coatings for chips |
Equipment Cost | Medium | Higher |
Environmental Impact | Low (green technology) | Moderate to high |
In short:
- Use PVD when you need a clean, decorative, or wear-resistant coating with precision.
- Use CVD when you need a strong, functional ceramic or complex layer — especially in electronics.
Real-Life Applications of Physical Vapor Deposition
PVD is kind of a superstar in the industrial world. It shows up in places you wouldn’t even expect! Let’s check out some common uses:
Electronics and Semiconductors
PVD is used to coat microchips, displays, and smartphone parts. It helps improve performance, conductivity, and even heat resistance.
Watches and Jewelry
Ever seen a black-coated watch that doesn’t scratch easily? That’s likely PVD! It’s used to give accessories a tough, colorful finish that lasts for years.
Automotive Industry
Car manufacturers use PVD coatings on trim, mirrors, gear knobs, and more. It helps protect against corrosion while making things look sleek and shiny.
Medical Devices
Surgical tools, implants, and dental equipment often have PVD coatings to stay sterile, durable, and smooth.
Aerospace and Defense
In high-stress environments like aircraft engines or satellites, PVD coatings help reduce wear and improve performance under extreme conditions.
Cutting Tools and Machinery
Drills, blades, and heavy-duty equipment benefit from PVD because it increases hardness and reduces wear.
Why Physical Vapor Deposition Is Here to Stay
The world is moving toward cleaner, more efficient technologies. And that’s exactly where physical vapor deposition shines.
Manufacturers love PVD because it:
- Cuts down waste
- Reduces costs over time
- Supports sustainable production
- Produces excellent results in less time
Plus, as more industries aim to go green, methods like PVD offer a smart way to balance performance with responsibility.
Even better, new innovations in nanotechnology and coating science are expanding what PVD can do. From solar panels to electric vehicles, it’s becoming the go-to method for high-tech surfaces.
Which Is Better: PVD or CVD?
Honestly? Neither is “better” — it all depends on what you need.
Choose PVD if you want:
- A clean, shiny, and precise finish
- Eco-friendly coating
- Lower temperature applications
- A more cost-effective solution
Choose CVD if you need:
- Complex ceramic or silicon coatings
- High heat tolerance
- Very specific electrical or chemical properties
The good news? Engineers and designers often use both PVD and CVD in different stages of making high-performance products. It’s not one or the other — it’s all about using the right tool for the job.
Wrapping It All Up
We covered a lot, but let’s keep the main takeaway simple:
Physical vapor deposition is a powerful, clean, and modern way to apply coatings that last. It uses vapor, not chemicals, to form thin, precise layers that improve strength, appearance, and durability.
Compared to chemical vapor deposition, it’s usually more eco-friendly, works at lower temperatures, and offers more control.
Both processes have their place in today’s world — but as industries move toward greener tech, PVD is becoming a favorite for many reasons.
Next time you wear a smartwatch, pick up a tool, or use your phone, there’s a good chance physical vapor deposition played a role. And now you know exactly how!