The Importance of Tooling in Custom Plastic Injection Molding
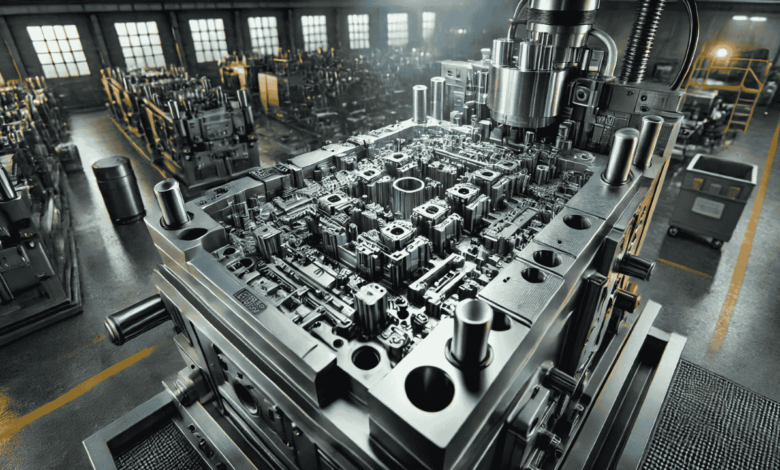
If we must confess to anything at all, it’ll be a true confession. What we’ll be confessing to is how custom plastic injection molding has reshaped complex part manufacturing. The impact is so immense you can’t begin to dream about it. Is it the high quality of parts or the frequency of production cycles? Let’s not forget the superb efficiency that results in cost reduction. Honestly, we can go on and on and we’ll still be talking about it. But one thing stands out, and that is the foundation of all these goodies being enjoyed by manufacturers. If you’re guessing what that is, it is the role of tooling, that is, the mold that makes all these a possibility. The mold confirms the quality of parts, the efficiency of the whole injection molding process, and most of all the total cost that’ll be incurred. As deserving of over-praise as the mold is, we’d like to tell you more about it. So please join us on this adventurous tale.
The Role of Tooling in Injection Molding
As we begin this journey, there’s one extra thing we need to mention, and that is the fact that many industries are confident of getting the best parts when custom injection molding is employed. In fact, your level of commitment toward investing in this prized tool determines the outcome of your manufacturing endeavor. So, what makes this mold so special you might ask? Here’s why. An injection molding tool carries the design for your intended products and is ready to transform the raw materials injected in it into your desired products. There’s more, injection molds have different features to them. Some of these are its cavities, where complex designs are crafted to form the shape of the desired product.
There are also the gates and runners, these represent the entry points and the flow paths of the melted plastic that conforms to the designs of the product. And then, there’s the cooling system as well. A fun fact about this cooling system is once the molten plastic is injected into the mold, it ensures proper and complete solidification of the plastic. In addition, it controls the temperature of the mold, keeping it at optimal functionality. Pardon our heavy technical jargon.
Let’s tell you some more about this gem of a tool. Do you know that when crafting a mold design, it is imperative to consider fabricating an accurate mold? That’s because the consequences of an inaccurate mold design are dire. Beginning with increased production cycles to product quality, and likewise irregularities in the product’s performance and presentation. Ultimately leading to more costs.
Tool Design and Production Efficiency
All that we’ve said so far has brought us to this point, which is where we put under a microscopic view those reasons why the mold works efficiently. Without wasting more of your time, the key word here is efficiency. Now what drives the efficiency of the mold? When something is meticulously designed, it means every contour and corner is deftly crafted. The same applies to the mold too. The design of this tool includes optimizing the location of its features. That begins with the cooling channel. A properly placed cooling channel for the mold will guarantee the balance of temperature that’ll, in turn, create top-quality parts.
The precision devoted to making a tool such as a mold is stronger than a basketballer’s shooting practice for accuracy. That is equally evident in the determination of manufacturers to reduce scrap rates and material waste. For this reason, they put a lot of attention on regulating injection pressure. That is also why they make sure the flow pattern of the material does not endanger the mold. When you think of designing a tool like the mold, do not just think of the present value, but also the future transformation of manufacturing. No wonder automated ejection features and mold inserts were developed. These have assisted many manufacturers in adjusting to changes during a cycle and not losing time.
One last thing, perspective matters even in tool design and production efficiency. What efficiency seems like to the manufacturer in terms of time and resource management is different for potential clients. In all, everyone wants efficiency.
The Impact of Mold Quality on Product Quality
Since we’ve discussed the impact of quality mold on production efficiency, we think it’s time we show you how it influences product quality. Let’s paint a picture for you. Just imagine your plastic household items. Imagine the perfectly shaped contours and surface finish, that didn’t fall from the sky. It is a work of art produced by a high-quality mold. Let’s take it a step further, shall we? When you get into your car and the features of the dashboard and some exterior parts gleam at you, you feel the excitement right? Those are deftly produced by top-quality molds. These are a few examples of what the automotive and consumer goods industries enjoy through plastic injection molding, now imagine its impact in other industries such as aerospace, medical, and industrial sectors. We can guess what you’re thinking already. This should tell you how much manufacturers invest in quality molds to serve you the best things in life. The surface finish, dimensional accuracy, and consistency are allowed for magnificently fabricated molds.
It doesn’t stop there. The materials used in making these molds also contribute immensely to their functionality. You guessed right, materials such as aluminum and steel are the best-fit materials to make a superior mold with excellent tight tolerance control. With such materials, the molds do not understand what depreciation means even after continuous use. Furthermore, maintenance of the molds also heightens their performance. The positive effect that gives production includes the elimination of defects like air bubbles, incomplete filling, and warping. So the next time you hold a plastic component, think of the top-notch molds that made them.
Conclusion
Overall, the importance of tooling in custom plastic injection molding cannot be overemphasized and the mold displays a manufacturing brilliance beyond words. From its impact on production efficiency to birthing quality products that are devoid of flaws which in turn minimizes costs, it is safe to say high-quality molds are the superheroes of manufacturing. However, apart from being the superheroes, they cannot effectively function without their sidekicks which are design precision and frequent maintenance. The greatest tools create the best experiences, and they are equally responsible for the numerous successes in the custom plastic injection molding world.