Cooling Tower Maintenance: Which Practice Helps It Work More Efficiently?
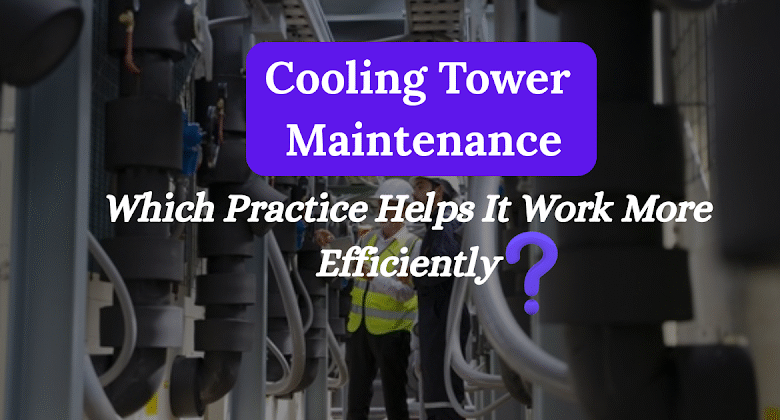
Table of Contents
- Introduction
- Why Installation and Design Matter
- Top Practices That Help a Cooling Tower Work More Efficiently
- Regular Cooling Tower Maintenance
- Water Treatment and Quality Control
- Routine Maintenance and Inspection
- Fan and Motor Optimization
- Drift Eliminator and Fill Media Cleaning
- Monitoring and Automation Systems
- Seasonal Maintenance Checks
- Weekly Maintenance Checklist
- Monthly Maintenance Checklist
- Quarterly Maintenance Checklist
- New Cooling Tower Considerations
- Common Issues and Solutions
- The ROI of Proactive Cooling Tower Maintenance
- Conclusion
If you’ve worked with industrial systems, you know just how important cooling towers are. They play a critical role in regulating heat and ensuring equipment operates smoothly. But like any system, their efficiency heavily relies on proper care, upkeep, and timely cooling tower repair. That’s where cooling tower maintenance comes in. Without it, you’re bound to face inefficiencies, costly breakdowns, and unscheduled downtime. Trust me, there’s no such thing as overestimating the value of regular maintenance.
Today, I’ll share the best practices to keep cooling towers running at maximum efficiency. From proper , here’s everything you need to know to get the most out of your cooling tower system.
Cooling Tower Installation and Design
Before diving into maintenance, let’s take a step back and talk about the foundation of your cooling tower’s performance: proper installation and smart design. A well-installed and thoughtfully designed cooling tower not only improves performance but also reduces the need for cooling tower repair, costly repairs, and downtime.
By getting it right from the start, you set the stage for uninterrupted operations, lower energy costs, and a longer lifespan.
- Installation Matters: Cooling tower installation isn’t just about assembling parts. It’s about setting the foundation for long-term efficiency. A poorly installed tower often leads to unnecessary repairs and performance issues down the road.
- Thoughtful Design: The design of critical components, like the water distribution system and fan blades, directly impacts performance. A well-designed system optimizes airflow and water distribution, ensuring heat is rejected efficiently.
- Material Quality: Whether you’re installing a new tower or replacing an old one, invest in quality materials that can endure wear, heat, and environmental conditions. The initial cost may be higher, but it saves money in the long run.
- Inspections During Installation: Conducting a thorough visual inspection during the installation process helps identify any potential problems before they escalate.
A solid installation sets the stage for better maintenance and seamless operation, ensuring your system runs efficiently and lasts longer. It’s the foundation for avoiding costly repairs down the line and maximizing performance.
Top Practices That Help a Cooling Tower Work More Efficiently
Regular Cooling Tower Maintenance
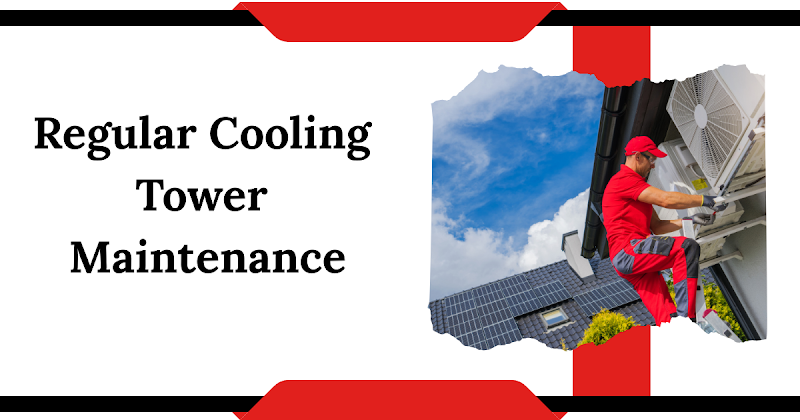
When I think about efficiency, proactive cooling tower maintenance is always top of mind. For me, this means regularly inspecting, cleaning, treating the water, and replacing parts to keep the tower running smoothly.
I’ve seen firsthand how proper maintenance can prevent issues like scaling, corrosion, and microbial growth. These cooling tower problems don’t just hurt efficiency, they can cause serious equipment failures.
Recently, we worked on a project where we discovered a cooling tower that hadn’t been inspected for two years. As part of the team, we conducted a thorough assessment, implemented necessary maintenance, and ensured it met safety and efficiency standards moving forward.
Water Treatment and Quality Control
Water is the backbone of any cooling tower. Managing water chemistry isn’t just good practice; it’s essential. Poor water quality can lead to scaling, biological fouling, and reduced efficiency.
Here’s the approach to handling water treatment:
- Regularly monitor pH, alkalinity, and calcium levels.
- Use chemical dosing systems to ensure proper treatment levels.
- Stay on top of biological control measures to prevent Legionella diseases and other harmful bacteria.
- Perform regular blowdowns to prevent mineral buildup and ensure clean water.
- Work with a qualified water treatment professional to analyze and adjust chemical parameters as needed.
Routine Maintenance and Inspection
Regular maintenance is essential to keep your cooling tower running efficiently and to prevent unexpected breakdowns. By routinely inspecting and servicing your cooling tower, you can improve its performance, extend its lifespan, and reduce energy costs. Here are some key areas to focus on:
- Clean out debris from the water basin regularly.
- Check for any cracks or leaks in the tower structure.
- Inspect motor, fan, and other mechanical components for wear and tear.
- Lubricate moving parts as needed.
- Regularly change air filters.
Performing these routine maintenance tasks can help identify potential issues before they become major problems, saving time and money in the
Fan and Motor Optimization
Did you know optimizing your fan and motor can dramatically improve air circulation and heat rejection? Often underestimated, this simple adjustment can enhance system performance, lower energy costs, and extend equipment lifespan.
Here’s what I recommend:
- Check fan alignment and belt tension regularly.
- Ensure motors are well-lubricated and running without strain.
- Inspect fan blades for dirt or damage that can affect performance.
Even small adjustments here can lead to big improvements in efficiency.
Drift Eliminator and Fill Media Cleaning
Debris buildup on drift eliminators and cooling tower fill media can greatly reduce the efficiency of a cooling tower. When left untreated, this accumulation decreases the surface area needed for effective heat transfer, resulting in poor performance.
To keep your cooling tower running optimally, regular maintenance is essential. A quarterly cleaning and descaling schedule is highly recommended to prevent issues caused by debris and buildup.
How to Do It Right Way?
- Inspect regularly: Check for debris on drift eliminators and fill media at least once a week. Use a flashlight to spot hidden buildup and remove debris with a soft brush or water spray.
- Clean quarterly: Perform descaling every three months by using a non-corrosive cleaning solution. Drain the system, apply the solution to remove buildup, and rinse thoroughly to prevent chemical residue.
- Optimize heat transfer: Ensure all surfaces, like the fill media and basin, are clean and obstruction-free. Use a pressure washer on low settings to avoid damaging delicate components.
- Prevent downtime: Schedule routine cleaning and maintenance on a calendar. Check fan alignment, water flow, and pump functionality during each cleaning session to catch issues early and avoid costly repairs.
Monitoring and Automation Systems
Modern technology has revolutionized maintenance for cooling towers, making it smarter and more efficient than ever. With IoT sensors, automated alerts, and predictive maintenance systems, you gain real-time insights into your cooling tower’s performance, enabling proactive decision-making. These systems allow you to track critical metrics like water flow rates, temperature, and energy usage while identifying potential issues before they escalate into costly repairs or downtime.
By automating routine checks and diagnostics, you not only save time but also extend the lifespan of your mechanical equipment and optimize operational efficiency. Embracing these advanced tools ensures your cooling tower runs smoothly, reduces unexpected failures, and ultimately saves money. Stay ahead with maintenance that works smarter, not harder.
Seasonal Maintenance Checks
Your cooling tower’s demands shift with the seasons, working harder during scorching summers and scaling down in colder months. Staying ahead with seasonal maintenance is key to keeping operations smooth and avoiding costly surprises. Regular upkeep not only prevents downtime but also extends the lifespan of your system. Here’s a breakdown of how to stay proactive with weekly, monthly, and quarterly maintenance checks:
Weekly Maintenance Checklist
- Inspect water levels and ensure proper flow rates.
- Check for debris buildup in the basin and remove it.
- Monitor pump operation to confirm consistent performance.
- Test water quality to prevent scaling, corrosion, or bacteria growth.
Monthly Maintenance Checklist
- Inspect the fill media for uneven wear and clean as needed.
- Ensure all fans, belts, and motors are functioning smoothly.
- Test chemical dosing systems to maintain water treatment balance.
- Check drift eliminators for damage or clogging.
Quarterly Maintenance Checklist
- Conduct a deep inspection during low-use periods to identify hidden wear and tear.
- Lubricate bearings and adjust any misaligned components.
- Inspect and recalibrate sensors or controls for accuracy.
- Assess overall structural integrity, including support beams and casing.
By sticking to this proactive schedule, you’ll keep your cooling tower prepared for peak performance in any season.
New Cooling Tower Considerations
Installing a new cooling tower is a major investment that can significantly impact your facility’s efficiency and operations. To ensure you make the right choice, there are several key factors to consider.
Start by assessing your specific cooling needs, what capacity and performance levels will your operations require? Next, think about energy efficiency.
By taking these factors into account, you can ensure your new cooling tower not only meets your needs today but also delivers long-term value.
- Prioritize energy efficiency and quality materials during tower construction.
- Work with a reputable installation service that offers competitive pricing but doesn’t compromise on quality.
Common Issues and Solutions
Cooling towers can face a range of common issues that impact performance and efficiency. Frequent problems include scaling, corrosion, biofilm buildup, and clogged nozzles, all of which can reduce cooling capacity and increase maintenance costs. Understanding these challenges and addressing them promptly is key to ensuring optimal operation and extending the lifespan of your cooling tower system.
- Scaling and bacterial growth due to poor water treatment. Implement a regular water treatment program and use appropriate chemical treatments to prevent scaling and bacteria.
- Debris buildup leading to reduced efficiency. Schedule routine cleaning and maintenance to remove debris and ensure smooth operation.
- Equipment failure when routine checks are skipped. Conduct regular inspections and servicing to identify and fix potential issues before they escalate.
- Corrosion causing damage to equipment. Use corrosion inhibitors and ensure proper pH balance in the system to reduce the risk of damage.
Solutions include regular cooling tower cleaning, proper water treatment programs, and preventive maintenance plans. Inspections and prompt corrective measures go a long way in optimizing performance.
The ROI of Proactive Cooling Tower Maintenance
Proactive cooling tower maintenance is essential for long-term cooling tower efficiency and cost savings. Here’s why prioritizing regular maintenance for your industrial cooling towers is a smart investment:
- Lower energy and repair costs: Well-maintained cooling systems operate more efficiently, reducing energy consumption and minimizing expensive repairs.
- Prevent downtime: Regular inspections and proactive servicing help avoid unexpected system failures that can disrupt industrial operations.
- Extend equipment lifespan: Proper maintenance ensures your cooling tower components last longer, delaying the need for costly replacements.
- Enhance environmental compliance: Keep your cooling system in line with environmental regulations by reducing water waste and controlling emissions.
- Improve workplace safety: A well-maintained cooling system reduces risks such as leaks, harmful bacteria growth (like Legionella), and unsafe working conditions.
The upfront investment in cooling tower maintenance services pays for itself through savings, efficiency gains, and greater reliability.
Conclusion
To sum up, there’s no better way to ensure your cooling tower operates efficiently than through regular cooling tower maintenance. Adding a robust maintenance routine to your operations doesn’t just enhance performance; it helps you save time and money in the long run.
From smart installation to regular inspections, water treatment, and automation, every maintenance step adds up to serious performance gains. Think fewer breakdowns, lower energy bills, and a system that runs like clockwork. This guide has walked you through exactly how to make that happen.
Now, it’s your move. Build your checklist, train your team, or better yet, consult with cooling tower maintenance experts to create a tailored plan that fits your system’s needs.
FAQ
Why is cooling tower maintenance important?
Proper maintenance prevents issues like scaling, corrosion, and biological growth, improves energy efficiency, ensures safety, and reduces long-term repair costs.
How often should cooling towers be maintained?
In large commercial buildings, cooling towers should be inspected monthly, with detailed cleaning and maintenance performed quarterly and annually, depending on usage, environment, and system type.
What chemicals are used in cooling tower water treatment?
Common chemicals include biocides (to kill bacteria), scale inhibitors, corrosion inhibitors, and pH adjusters, depending on water conditions and system needs.
How to make a cooling tower more efficient?
To make a cooling tower more efficient, perform regular maintenance, optimize water treatment, clean fill media and drift eliminators, ensure proper airflow by maintaining fans and motors, and use automation systems for real-time performance monitoring.
What is the most efficient cooling tower system?
Counterflow induced draft cooling towers are considered the most efficient due to their vertical airflow design, compact footprint, and enhanced heat exchange. Systems with variable frequency drives (VFDs), high-efficiency fans, and automated water treatment offer even greater performance and energy savings.