Revolutionizing Manufacturing Quality Inspection with Continuous Sheet Anomaly Detection
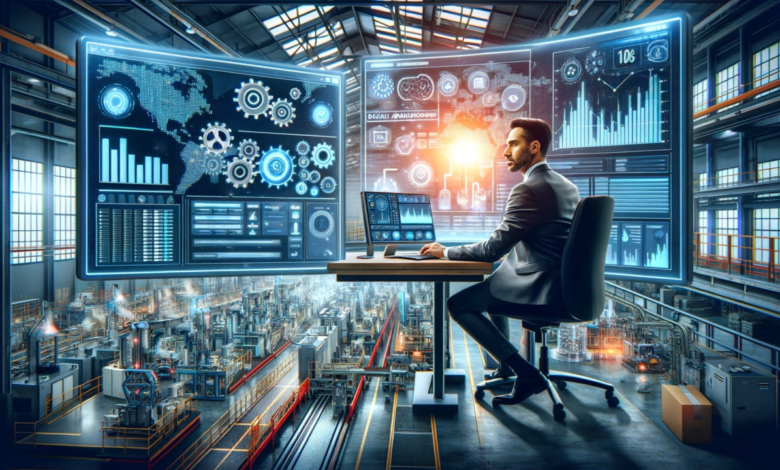
Continuous sheet inspection plays a pivotal role in manufacturing industries that produce materials like metals, textiles, films, paper, glass, and plastics in rolls or sheets. This process enables the real-time detection of anomalies—defects or irregularities—ensuring that only high-quality products reach customers while reducing waste. Advanced imaging and automation technologies form the backbone of these inspection systems, driving quality assurance and operational efficiency.
Technology for Automating Continuous Sheet Inspection
The automation of continuous sheet inspection requires the seamless integration of four core elements: imaging solutions, lighting, AI-powered software, and external support systems. These components collaboratively ensure accurate anomaly detection, even in fast-paced production lines with diverse product specifications.
Imaging Solutions
A robust imaging solution is the cornerstone of any continuous sheet inspection system. The choice of technology depends on factors such as sheet width, defect size, material properties, and production line speed.
Line-Scan Machine Vision Cameras
• Technology: Line-scan cameras work by capturing images line by line as the sheet moves. These lines are combined to create a detailed 2D image of the sheet, ensuring no data loss even at high speeds.
• Applications:
• Ideal for high-speed production lines.
• Commonly used for inspecting textiles, metals, and films.
• Selection Factors:
• Resolution: Detecting small defects (<1 mm or micron-level) requires 8k or 16k line-scan cameras.
• Working Distance and Field of View (FoV):
• Shorter working distances improve detail capture but reduce FoV.
• Wide sheets may necessitate multiple cameras for complete coverage.
CIS (Contact Image Sensors)
• Technology: CIS modules, tailored to the sheet’s width, provide detailed imaging at close working distances (15–35 mm).
• Applications:
• Suitable for reflective materials like foil, aluminum coatings, and smooth surfaces.
• Unsuitable for rough or vibrating materials.
• Advantages:
• Enables seamless edge-to-edge inspection.
• Customizable lengths for varying sheet widths.
Selecting the Right Imaging Solution
The choice depends on:
• Material Properties: Reflectivity and surface texture.
• Defect Size: Micron-level or larger anomalies.
• Line Speed: High-speed lines need high-resolution imaging.
• Sheet Width: Wide sheets often require multiple imaging devices.
Lighting
Lighting significantly influences the quality of captured images, and its configuration varies based on material type, defect characteristics, and desired precision.
Key Lighting Considerations
• Material Reflectivity:
• Shiny materials require adjustments in lighting angle and intensity to minimize glare.
• Diffused lighting softens reflections and enhances contrast.
• Defect Visibility:
• High-intensity lighting improves small defect detection.
• Backlighting highlights defects such as cracks or holes by creating stark contrasts.
• Lighting Setup:
• Angle and Diffusers: Adjusted to enhance texture visibility and reduce harsh reflections.
• Intensity: Optimized to match sensor sensitivity.
Appropriate lighting setups amplify defect clarity, enabling consistent and accurate anomaly detection.
Software and AI Algorithms
The software is the brain of the inspection system, converting captured data into actionable insights by identifying and categorizing anomalies.
AI-Powered Anomaly Detection
• Dynamic Defect Recognition:
• AI models analyze images, differentiating actual defects from shadows or acceptable variations using pre-trained data.
• Custom Thresholds:
• Thresholds allow manufacturers to accept minor deviations. The software adheres to these specifications during inspections.
• Advanced Performance:
• Proprietary software like Intelgic’s integrates AI and machine vision to identify a wide range of defects across materials and processes.
Key Features
• Real-Time Analysis: Flags or corrects defects instantly.
• Scalability: Models adapt to new defect types and production changes.
• Defect Categorization: Provides actionable insights by classifying defects by size, type, and severity.
External Support Systems
To operate effectively in real-world manufacturing, vision systems require external electromechanical support to optimize performance.
Customized Support Systems
• Multi-Product Adaptability:
• When inspecting varied products, operators can dynamically adjust camera positions and lighting configurations. Automated systems ensure consistent inspection for all product types.
• Vibration Mitigation:
• Vibration dampening is essential, especially for CIS systems operating at close distances.
• Robotic Integration:
• Robots may dynamically adjust cameras, align products, or flip sheets for double-sided inspections.
• Process Adaptation:
• Systems are designed to integrate seamlessly into existing workflows, ensuring compatibility with manufacturing processes.
Achieving an Integrated Inspection System
The successful deployment of a continuous sheet inspection system relies on the harmonious integration of its key components. High-quality imaging captures critical data, optimized lighting enhances defect visibility, intelligent software analyzes and categorizes anomalies, and external systems ensure seamless adaptation to production environments. Together, these technologies create an efficient, scalable, and precise inspection solution that meets the evolving demands of modern manufacturing.
The Road Ahead for Continuous Sheet Inspection
Continuous sheet inspection remains indispensable for ensuring stringent quality standards in manufacturing. Leveraging advanced imaging, machine vision, and real-time analysis enables early defect detection, minimizing waste while enhancing operational efficiency.
In the years ahead, innovations like micron-level detection, ultra-high-resolution imaging, and increased automation are set to revolutionize this field. By addressing the rising demands of quality-focused markets, continuous sheet inspection will remain a cornerstone of manufacturing excellence, paving the way for enhanced precision and productivity.