Efficient Injection Molding Manufacturing & CNC Machining Plastic Parts
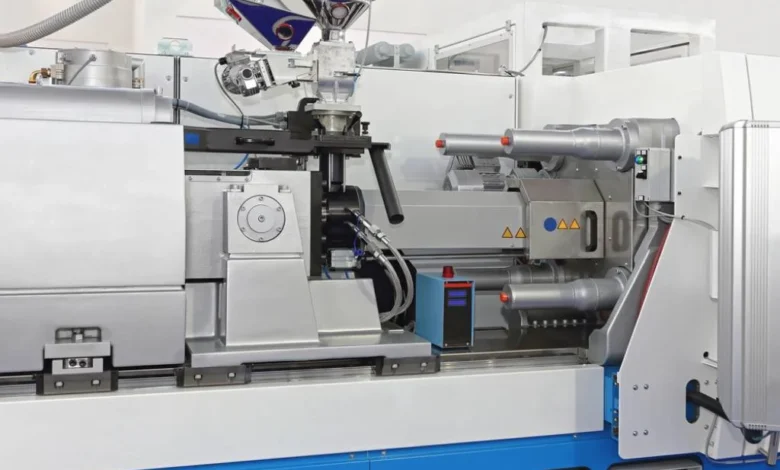
Table of Contents
- Introduction to Efficient Injection Molding & CNC Machining
- The Advantages of Utilizing the Two System Integration of Injection Molding and CNC Machining
- Key Factors for Success in Plastic Parts Manufacturing
- Injection Molding and CNC Machining Working Together Efficiently
- Applications in Different Industry Spheres
- Conclusion
It is basically described as a process of combining precision injection molding and CNC machining techniques for the production of superior-quality plastic components. This kind of manufacturing is efficient because it leads to quick production along with narrow tolerances and waste that is very minimal; thus, it is applicable for both the production of very high-volume and complicated kinds of parts with great performance in industries.
Are you looking for precision and speed in the production of plastic parts? “Efficient Injection Molding Manufacturing and CNC Machining” means both the price and high-quality production of very complex designs in large numbers.
Efficient Injection Molding Manufacturing & CNC Machining combines the process of manufacturing high-precision plastic parts with the streamlining of such works. Typical of a combination of injection molding with speed and CNC machining with accuracy, short turnaround times are guaranteed with minimal waste.
The Advantages of Utilizing the Two System Integration of Injection Molding and CNC Machining
Combined efforts such as these would differ in terms of the products produced by the synergy of injection molding and CNC machining rather than costs for manufacturers. Here are some of the major advantages:
1. High Efficiency and Reduced Lead Times
Injection molding fast-tracks production on parts that CNC machining refines and finishes to perfection. Thus, delays are greatly minimized, speeding up the whole manufacturing process.
2. Cost Savings for High-Volume Production
Injection molding involves high up-front costs for mold preparation, but that pressure goes away when running big quantities. CNC machining reduces wastage and guarantees the accuracy of every unit, thus improving overall cost efficiency.
3. Increased Precision and Detail
CNC machining allows fine-tuned control over the dimensions of the parts by allowing intricate designs and precision finishes. In instances where the production of parts requires tight tolerances, for example, gears, medical components, and aerospace parts, such precision becomes very important.
4. Complex Geometry and Customization
CNC machining allows properties of far more complex geometries and customization than traditional molding methods alone. This readily allows specific features to be incorporated or part designs to be fine-tuned, all without adversely affecting the production efficiency.
5. High Surface Finish
When injection molding is employed alone, sometimes its products bear poor surface finishes, especially when very intricate designs are involved. CNC machining eradicates those imperfections and produces a part adhering to the highest parameters of quality and functionality.
Key Factors for Success in Plastic Parts Manufacturing
CNC machining Plastic parts manufacturing success starts with the careful selection of materials. The right material must be selected, depending on the nature of the application (heat resistance, flexibility, or impact durability). Properties of the material must be studied to work best for performance and cost.
Another facet crucial to success is proper mold design and tooling. A high-grade mold must be used during production, which means an understanding of its quality and design to handle the complexities of plastic part geometry with the view of reducing wastage and achieving consistency of all in a given operation. Proper tooling guarantees that production processes run smoothly with timeliness and little error.
Injection Molding and CNC Machining Working Together Efficiently
Injection molding and CNC machining integration in one system will ensure maximum efficiency in the production of plastic parts by complementing each other. Injection molding shall mass-produce parts that have a consistent shape and size. CNC machining shall then tweak, test, and customize them. This is how they mutually benefit each other:
1. All for Mass Production
Injection molding is ideal for a mass production level of parts having the same shape and form. The designing of the mold must come first; prior to injection molding, it will make matching parts in high volume with minimal variation.
2. CNC Machining for Accuracy and Customization
Post-mold CNC machining serves these components to fit their needs accurately. CNC machining provides the best route for functional and aesthetic improvement of molded parts, whether it is for maintaining tight tolerances, surface finishing, or custom modifications.
3. Prototypes and Testing
CNC machining is an important factor in making prototypes during the early performance stages of production. Before any large-scale injection molding production, prototypes can test designs and materials and, therefore, save time and costs.
Applications in Different Industry Spheres
Injection molding and CNC machining are highly sought after in manufacturing for high-volume production with accuracy.
All the following applications are when injection molding is combined with CNC machining:
- Automotive Industry: Injection and CNC machining are complementary processes for producing long-lasting and complex automobile parts, such as dashboards, exterior and interior components, and engine parts. They produce parts that have to withstand very high stresses and temperature variations while maintaining very high precision.
- Medical Devices: Medical parts require extremely tight tolerances and a high degree of reliability. From surgical instruments to drug delivery devices, these parts are subject to many regulatory standards for volumes. The volume is supplied with injection molding while conforming to all specifications and tolerances by CNC machining.
- Consumer Electronics Consumption: This is highly dependent upon precision components in devices such as wearables, smartphones, and notebooks. Housings undergo injection molding, while smaller parts such as buttons or connectors may go through CNC machining refinement.
Conclusion
This unrivaled answer for the mass production of high-quality, durable plastic parts consists of plastic injection molding manufacturing coupled with CNC machining. Both have their enhanced precision and speed of production, making them a fitting choice for industries that absorb such demand for high bulk production and custom-designed parts. By selecting the best material for their applications, designing molds excellently, and expertly integrating all the processes, manufacturers would capitalize on maximized savings in cost and achieve great quality.
However, that is possible with the modern injection mold development and CNC manufacturing changes. The impact reaches from segment to segment, whether automotive, medical, or electronics, because it is truly innovative in present-day manufacturing.